Furnace Heat Reading Solution - Case Study
The client is into the business of manufacturing and repairing casting pots/molds.

Brand: Leading Client in the Manufacturing Industry

Industry: Casting

Location: India
Core Platform: IoT| Arduino
Programming Language: Python, Flask, Arduino C#
Hardware/Sensors: Arduino, ESP8266, HT 4068 High-temperature SiC, High Capacity Single Point Load Cells

Steel Industry

Across India, Iran, South Africa, and Africa.
Challenges
- Finding a sensor that can work at high temperature
- The ability of the sensor to work under dust and magnetic force environment
- Accuracy in results
- Find the high capacity load cell sensors
- Temperature sensors (up to 1800C ).
Strategic Approach
The client's requirements were feasible, the only challenge was to identify the high-level temperature and load sensors.
The analysis began with understanding the complete casting process, and what are the infrastructure involved, what is the manual and automatic process they follow. The problem and challenge were that they were not aware what is the accurate temperature of the casting mold, as they needed to use some manual process that can be dangerous and can blast the mold/pot if proper cooling down does not happen before the next work. So they were looking for a sensor that works on high temperatures like 1800 degrees Celcius or more and works with the magnetic environment.
We then gathered detailed requirements from the client about how many variations of their existing furnaces were present, what kind of temperature variations are applicable for threshold and alerts. The range of empty furnace weight to filled furnace weight in identifying the furnace, etc to ensure we are building the right application
Before the actual project started we collected the following documentation to ensure we are building the right application:
- RFP
- SOW
- Design documents
- Sample Data/Physical Printed Forms of current manual process
- Organization hierarchy and its possible accessibility
- Solve the main problem of user engagement in checking temperature frequently.
- To get alerts and wastage logs of loaded metal vs melted metal.
- To identify the quality of metal scrapes
- Let the operator get the smart alerts for deciding the metal is melted or not
- To minimize the risk of hazards and provide a temperature reading from the furnace
- Identify load added to melt vs melted.
- Read the furnace's inside temperature
- Find wastage from the loaded metal vs melted metal
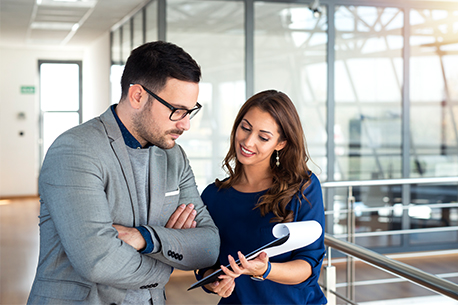
Project Development
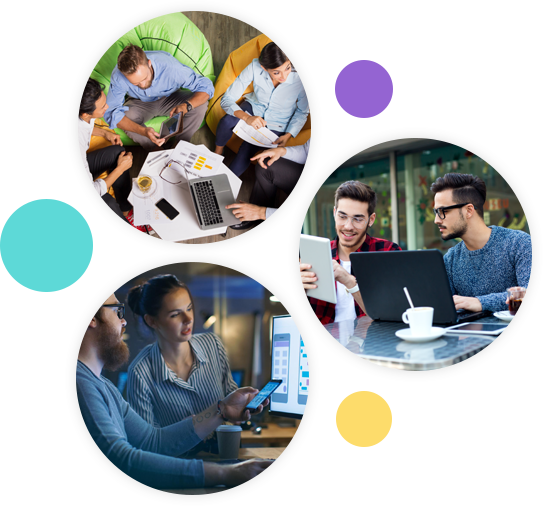
The project team comprised of developers
IoT Developer
Python developer
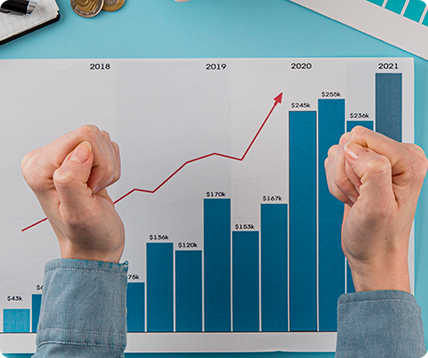
Scope:
- Develop a system that can identify the temperature of the furnace during the melting process
- Identifying loaded scrap vs melted metal's weight
- Finding the quality of scrap.
Timeline: 3 Months
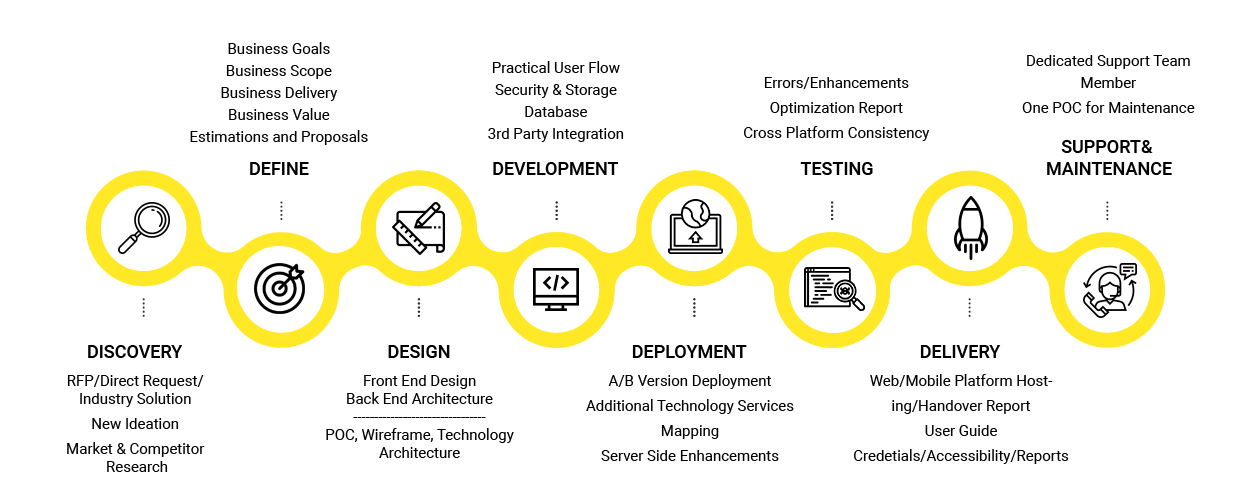
Project Highlights
Application Features
- Reading the furnace's inside temperature
- Finding wastage from the loaded metal vs melted metal
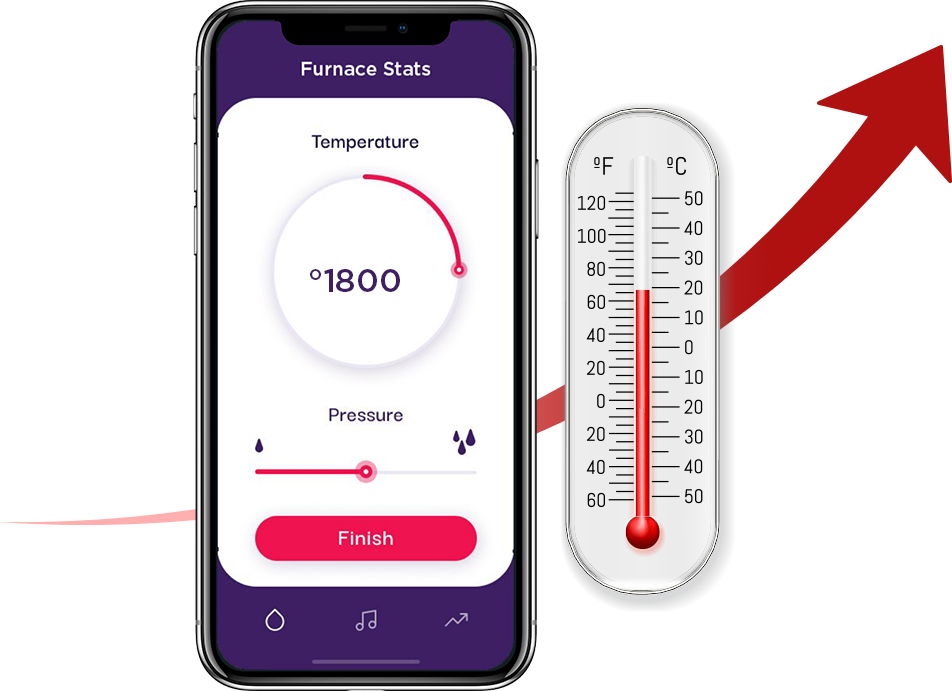
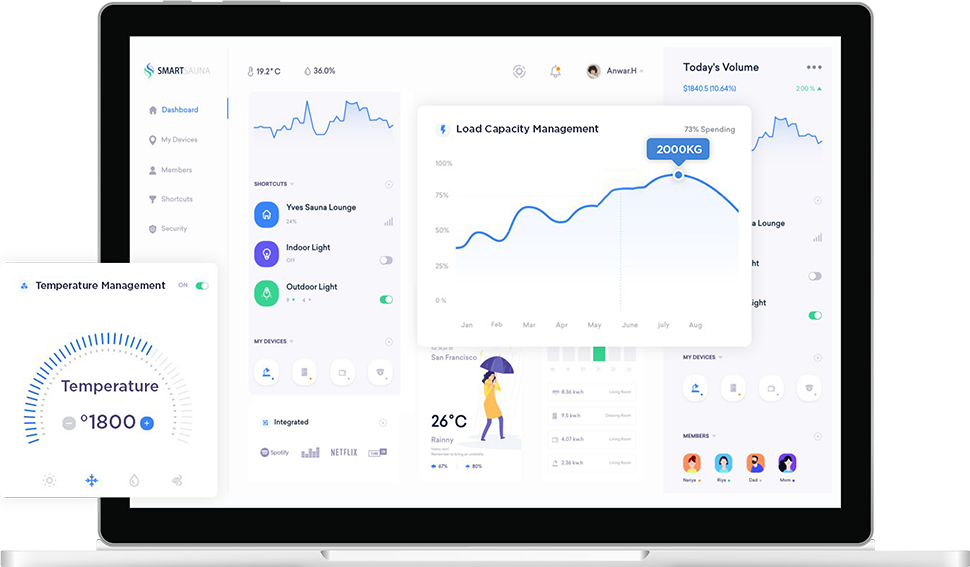
Key Highlights
- Handling 1800c temperature
- Handling almost 2000 KG load
- Identifying the right supplier of scrap.
Key Takeaways and Learnings

As Scrap and objects were coming with sand/water, the weight of actual metal appeared more.

During the melting process, the quality of scrap can be identified using automation.

The existing temperature sensors were quite costly and it was required to use more than 3-4 sensors in a single cycle of melting.
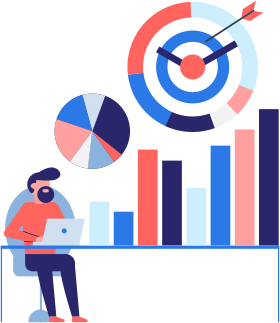
Business Impact
- The development of this app has resulted in Increasing efficiency, monitoring, control
- Calculation over the actual consumption of material and output(production) was done accurately.
- A dramatic impact was observed in the reduction of accidents
- Reduced the cost and increased the efficiency of the risk management strategy of the company.